Details
Fuel Gas Treatment Modular Skid Design
Fuel gas conditioning systems typically consist of a scrubber vessel or knock-out drum, filter-separator, heaters, pressure reduction, emergency/operational valves, and (flow) metering. The systems are often placed downstream of the production header or glycol contactor/separator. Fuel gas conditioning systems protect gas-fueled engines and turbines from over-pressure, liquids, solids and aerosols. Fuel gas first enters a scrubber or knock-out drum to remove liquids entrained in the gas, which can cause condensates to form due to the adiabatic cooling effect of the pressure reduction. In some cases, pre-heating is required before the gas pressure is reduced to the level required by the end-user. After the pressure has been reduced by means of pressure control valves, the gas is channeled to the filter-separator to further remove any liquid as well as solid particles.
If produced gas is left untreated before entering the combustion chamber of gas driven generators, it can result in major damage. Even small amounts of liquids and/or solids or over-pressurized gas entering the combustion chamber will have detrimental effects. Our systems are designed to protect gas-fueled engines and turbines from over-pressure, liquids, solids and aerosols. Furthermore, heating the gas properly above the dew point of the water and hydrocarbon prevents liquid condensation in the combustion chambers.
.png)
The package design typically consists of a scrubber vessel or knockout drum, filter-coalescer units, heaters, pressure reduction valves, emergency and operational valves, and (flow) metering, and is often placed downstream of production header, glycol contactor or separator for conditioning. Depending on the feed gas inlet conditions, fuel gas systems may be equipped with heaters or coolers. Frames Fuel Gas Conditioning Systems use pressure control valves to reduce the pressure of the production gas to the level required by the user. The resulting adiabatic cooling effect can cause condensates to form. Liquids entrained in the gas and condensates will be scrubbed to avoid any liquid carry-over into downstream equipment. The gas is channeled to the filter-coalescer units to further remove any liquid carry-over as well as solid particles. In some cases, pre-heating is required before the gas is let down. During the final steps of the process, the gas can be superheated to ensure temperatures above the dew point far downstream, ready for delivery to the consumer.
.jpg)
Project Management At Frames, we understand that success depends on sharp project management. As our client, we are driven to supporting your business, with our dedicated project team always on hand for one-onone contact, providing you with the best possible service. From concept through to design, production, testing and delivery, our project team will know your operating environment, and will use the latest technology to precisely meet your needs. We are solution orientated, understand your industry and always use strict document control and professional planning to exercise tight process control and meet all delivery deadlines. Our global office network, international supply chain and partnerships with leading vendors mean we are always able to supply the best systems and meet all of the local requirements and regulations.
Technical Details
• Materials ranging from carbon steel to alloys, such as super
duplex, Hastelloy and Inconel.
• Process piping designed to code, such as ANSI, fabrication to
ASME Section IX
• Vessels designed to code, such as ASME / PED / PD5500 &
National Board Registered (U-stamp) when required
• Instrumentation tubing, also used as process piping
• Valves including control and operation (ESD, PSD, switch-over)
• Electric process heaters with withdrawable elements or cast
heaters with exact heater duty calculations
• Certified for use in Zone 1 or Class 1
• Compact duplex configuration filter-coalescer units for
continuous operation
• Filtration fineness down to 1 micron and efficiencies up to 99.9%
• Pressures up to 400 bar(g) or higher upon request
Fuel-Gas Conditioning System Using JT
The Fuel-Gas Conditioning System is a unique, skid-mounted hybrid unit designed to remove water and high BTU’s for compressor fuel and instrumentation gas, but is not limited to small well streams. We have these systems in a number of applications from polishing gas, to processing rig fuel, or more commonly utilized at compressor gathering points.
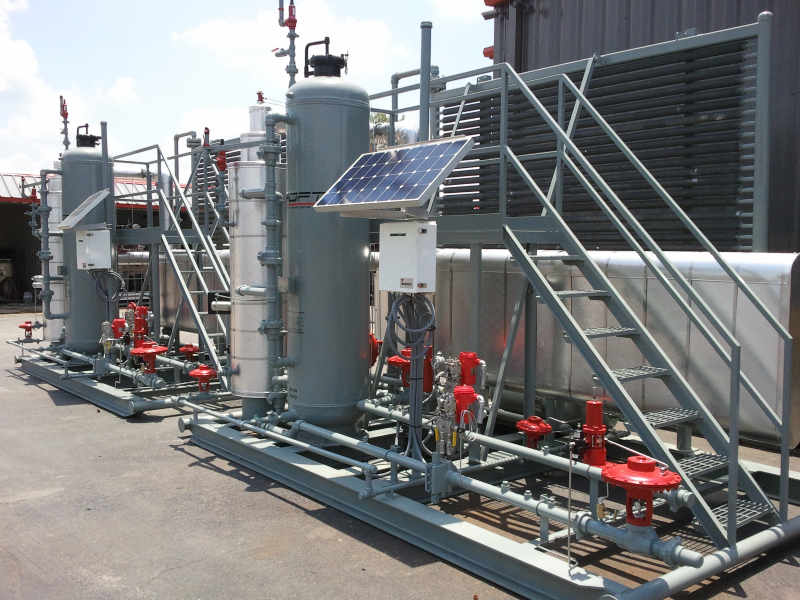
The Fuel-Gas Conditioning System is a combination of multiple systems combined into one package to condition fuel, supply, and instrument gas on location. The Fuel-Gas Conditioning System incorporates the Ambient Cooling System to initially cool the gas. The Joule Thomson System then removes hydrates and hydrocarbon liquids, lowering the BTU and reducing the water dew point. Lastly, the Passive Dehydration System further reduces the dew point well below the pipeline specifications using spa ex series desiccant.
View more about Fuel Gas Treatment System on main site